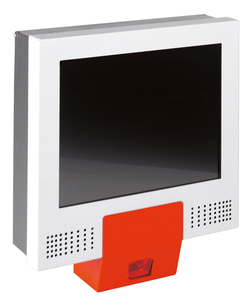
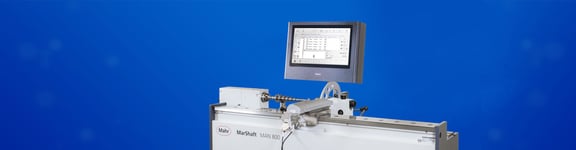
So vielfältig sind die Einsatzmöglichkeiten
Anwendungen der tci-Systeme
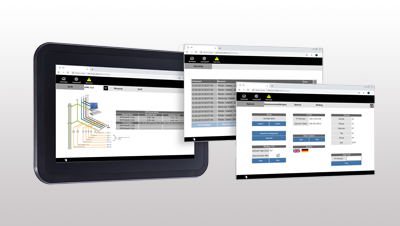
Energiemanagement
Nur wer seinen Energieverbrauch genau im Blick hat, kann das Potenzial für Einsparungen erkennen und den optimalen Einsatz steuern. Dazu müssen eine Vielzahl von Messstellen erfasst und mit detaillierten Datenanalysen ausgewertet werden. Dafür wurde das E10A von tci entwickelt.
Eigenschaften:
- AutomationBrowser
- durchgehenden Echtglasfront in Schutzart IP54
- 10.1“ PCT-Glastouch
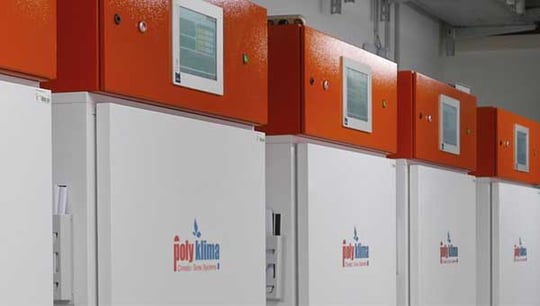
Klimatechnik
PolyKlima produziert Klimaschränke und nutzt das C120 in der Schaltschrankfront zur Einstellung und Überwachung. Neben der Temperatur werden Parameter wie Lichtintensität, Luftfeuchtigkeit oder die Gas-Sättigung überwacht und gesteuert.
Eigenschaften:
-
Montage in der Schalttafel IP65
-
Besonders robuste Ausführung
-
Resistiver Touch, mit Handschuhen bedienbar
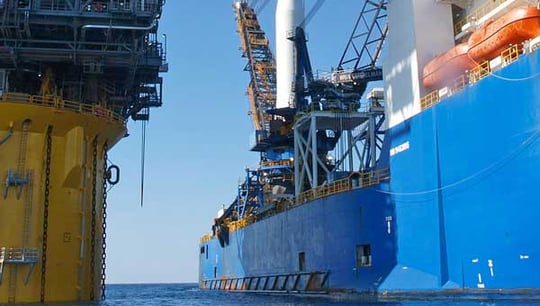
Marinetechnik
Mit bis zu 900.000 Tonnen Wasserverdrängung verlegen die Schiffe Pipelines oder werden zum Abbau von Öl- und Gasplattformen genutzt. Panel-PCs der A15-Serie sorgen dafür, dass Betriebszustände zuverlässig erfasst, angezeigt und an übergeordnete Systeme weitergeleitet werden.
Eigenschaften:
- robustes Gehäuse zur Schalttafelmontage
- besonders geringe Einbautiefe
- wasserdichte IP65-Front
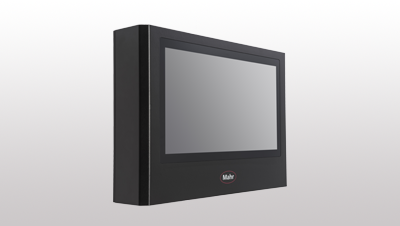
Fertigungsmesstechnik
Die Qualitätssicherung des Kunden wurde von manuellen Messungen auf eine automatisierte Lösung umgestellt. Gefordert war ein rundum geschlossener Panel-PC mit einer hohen Rechnerleistung und in robuster Industriequalität. Da bei der K-Serie von tci die Gehäusefarbe wählbar war – dazu noch mit Aufdruck eines individuellen Firmenlogos – fiel die Entscheidung auf einen K16-PC.
Eigenschaften:
- TFT zur Tragarm- oder Wandmontage
- Schutzart rundum bis IP54 skalierbar
- individuelle Gehäusefarbe und ein Logo-Aufdruck (auch bei Kleinserien)
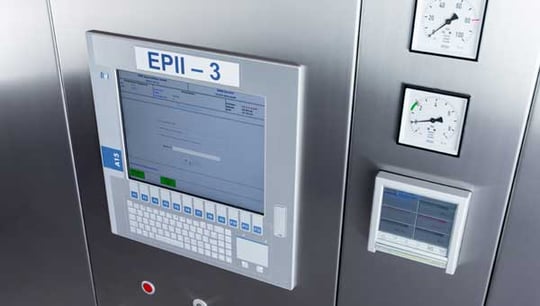
Hygiene-Bereich
Die Sterilisatoren unseres Kunden funktionieren vollautomatisch und können von 50 Liter bis 15.000 Liter (5 Paletten) eingesetzt werden. Die Vollautomaten können die keimfreien Teile nach dem abgeschlossenen Sterilisationsprozess sofort in den Verkehr bringen. Sie erfüllen unter anderem sämtliche Anforderungen der aktuellen DIN ISO EN 1422 und so fiel die Wahl schließlich auf den leicht zu reinigenden A15-PC.
Eigenschaften:
- kompakt
- robust
- IP-Schutz
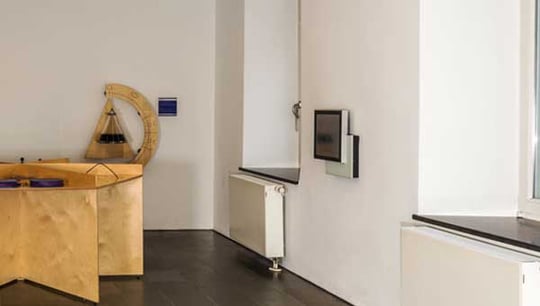
Besucher-Terminal
Das Mathematikum in Gießen wird jährlich von etwa 150.000 Menschen besucht. Das Prinzip ist "Mathematik zum Anfassen", und die Besucher tun das auch: sie fassen die über 180 Experimente nicht nur an, sondern gehen außerordentlich robust damit um. Der ambiento-PC sowie alle Gebäude-Systeme von tci sind genau darauf ausgelegt.
Eigenschaften:
- gute Usability
- Stabilität
- Langzeitlösung
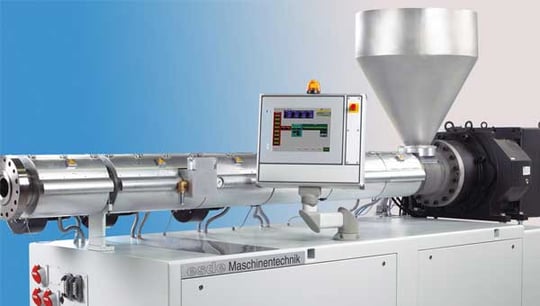
Maschinentechnik
Manche Maschinen laufen 10 Jahre und länger. Da muss auch die Steuerungstechnik auf eine möglichst lange Laufzeit ausgelegt und reparaturfreundlich sein. Erschütterungen, Vibrationen und weitere externe Einwirkungen haben keinen Einfluss auf die Funktion der A-Serie.
Eigenschaften:
- robust (Staub, Wärme)
- langlebig
- zuverlässig
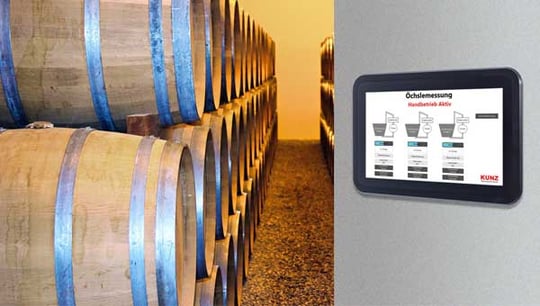
Automatisierungsanwendungen
Ob in der Gebäudetechnik oder dem Weinbau - wenn es um flexible Automatisierungslösungen geht, ist die E-Serie unschlagbar. Die Systeme können im Schaltschrank montiert oder am Tragarm befestigt werden.
Eigenschaften:
- Portierbarkeit der Applikation
- leicht zu reinigen durch Echtglasfront
- einfache Bedienbarkeit
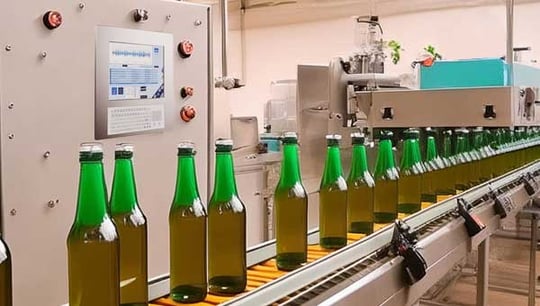
Lebensmittelproduktion
Bei der Herstellung von Lebensmitteln - wie zum Beispiel an Getränkeabfüllanlagen - müssen besonders hohe hygienische Anforderungen erfüllt werden. Der Touchpanel A19-PC sorgt für eine verlässliche Produktion.
Eigenschaften:
- leichte Reinigung
- einfache Bedienung
- ausfallsicher
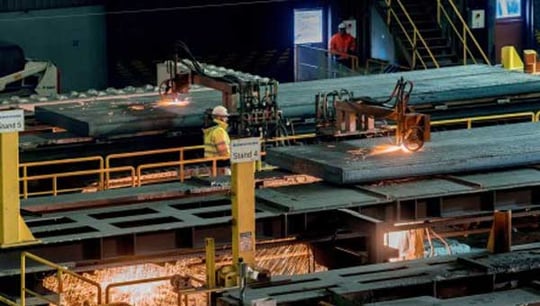
Stahlwerk
In einer riesigen Verladehalle werden Stahlrollen und Rohre durch mehrere Portalkräne auf Güterwagons verladen. In diesen Portalkränen sind die T15-VGA an Tragarmsystemen als Bedienterminals eingesetzt.
Die Kranführer bestätigen auf den Touch-Systemen die Verladevorgang. Der Datenaustausch in der gesamten Halle ist über WLAN realisiert. An jedem Ladekran wurde daher ein Box-PC als abgesetzte Lösung mit dem T15-VGA verbaut.
Eigenschaften:
- rund um die Uhr zuverlässig
- einsetzbar in rauen Umgebungen
- abgesetzte Lösung
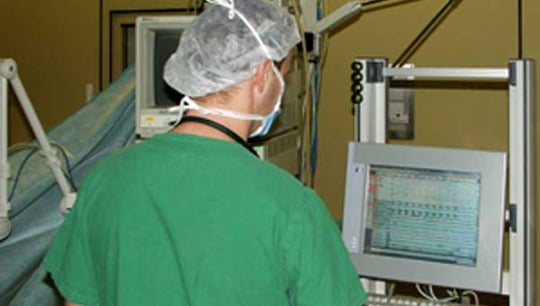
Medizintechnik
Die Abteilung für medizinische Informationstechnologie (MIT) suchte innerhalb der Umsetzung des Projektes Care Vue (Intensiv- und Narkosedokumentation) eine Hardwarelösung für die Intensiv- und Narkosedokumentation. Die Produkte des IPC-Herstellers tci aus Heuchelheim/Giessen haben sich bereits in vielen Umgebungen bewährt.
Eigenschaften:
- gute Wartbarkeit
- geringe Wärmeabgabe
- lautlos
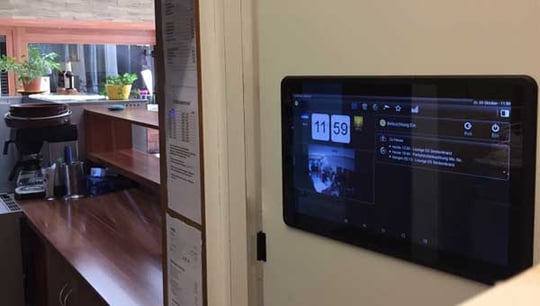
Hotel und Gastronomie
Unser Kunde hat ein System Schaltschrankeinbau im Servicebereich des Hotels Adlerhof eingebaut. Mithilfe des zentralen Panels können die Mitarbeiter die technische Infrastruktur des Hotels digital steuern. Verbaut wurde das Panel im Schaltschrank hinter der Theke und dient hauptsächlich der EIB Schnittstelle und Visualisierung der IP Kamera.
Eigenschaften:
- durchgehende Echtglasfront
- einfache Montage im Schaltschrank
- High Performance CPU